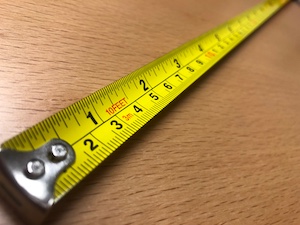
Successful ergonomics improvement programs include at least these 4 steps:
- Identifying Potential Ergonomics Issues
- Ergonomics Assessment Tools
- Controlling Ergonomics Risks
- Cost Justifying Ergonomic Improvements
If your injury logs include overexertion injuries like strains or sprains, musculoskeletal disorders like tendonitis or carpal tunnel syndrome, or even first-aide requests for pain relief, you’ve already identified potential ergonomics issues — Step 1.
Other signs of ergonomics issues include production bottlenecks and quality challenges, because they can often be traced back to a mismatch between worker capabilities and job requirements.
It’s not uncommon to find that roughly 30% of your HSE losses are caused or aggravated by ergonomics issues (see How to Budget for Ergonomics for more). Fortunately, these injuries and production barriers are preventable, and Step 2 — selecting the right Ergonomics Assessment Tools — is how you identify and control root causes.
An Ergonomics Management System should include standardized assessment tools (methods like NIOSH Lifting Equation, RULA, etc.) to identify and assess workplace ergonomics risk. Standardizing on a set of assessment tools that address your company’s specific types of work tasks, work environments, operating regions and working populations is key to success.
The tools you choose to standardize may also depend on the maturity of your ergonomics improvement process. In our guide, 5 Essential Elements of a Successful Ergonomics Process, we review the typical path companies go through as their ergonomics program matures from reacting to injuries (a trailing risk indicator) to measuring leading risk indicators and leveraging continuous improvement to prevent injuries and improve production metrics. Some are merely checklists, others are methods that produce a risk score (see Ergonomics Analysis: Checklists vs. Assessments for more).
Benefits of Standardizing Your Assessment Methods |
Consistency |
Repeatability |
Minimizes and focuses training requirements |
More meaningful “apples to apples” comparisons when prioritizing ergonomics risk and preparing management reports |
There are many ergonomics assessment tools to choose from. Some are evidence based, meaning they’re backed by published scientific research to verify their ability to predict risk. Others are not. Some are recommended by regulation, depending on your operating regions. Some are simplified and can be applied quickly, yet lack the power to accurately predict risk. Others are so complex they take too much time, or require too much training, to justify their broad use.
It’s wise to standardize on a subset of assessment tools that apply to specific task types. Doing so allows you to focus your team training efforts and create a consistent, repeatable process that delivers comparable before-and-after metrics.
In general, the simpler an assessment tool is to apply, the less specific and accurate it will be at uncovering root cause. Simplified tools can still be quite useful, however, because they can help you quickly identify and fix “low hanging fruit,” proving the value your workplace ergonomics process will bring, freeing additional resources as you grow the process.
Injury data is often organized by body part, so there’s a natural tendency to view ergonomics from that same perspective — “will this task increase injury risk for that body part?” However, since ergonomics related injuries often develop over time, and are caused by a combination of factors tied to work activities, most assessment methods are task-based, by necessity. For example, the NIOSH Lifting Equation applies only to lifting tasks; the Strain Index applies only to tasks involving the hand/wrist/lower arm; the Ohio Push-Pull Guidelines apply only to pushing and pulling tasks; and so on (see Guide to Picking the Best Ergo Analysis Tool for the Job for more). There are ergonomics assessment methods that focus on body parts, but they may lack specificity and accuracy.
Fortunately, the results of task-type assessments are easily mapped to body parts. For example, if the NIOSH Lifting Equation estimates a high risk, that maps to higher injury risk for the low back.
If you’re just getting your ergonomics assessment process started …
If you’re just getting started, keep things simple by selecting only one or a few assessment methods. If you have a lot of lifting tasks, for example, perhaps start by focusing only on lifting. Don’t try to do everything at once; instead do a few things well to gain experience and prove concept. Demonstrate some low-cost, high-value improvements to gain traction. As your process matures, you can selectively train your teams and grow your ergonomics assessment toolbox to fill in any gaps.
If you have a standard assessment process, but it’s not working …
There are a lot of reasons a process can fail. When it comes down to assessment methods, the most common complaints we hear are:
- The assessment method [or system] we use …
- is overly sensitive — it says everything’s a high risk!
- doesn’t apply well to the types of work tasks we do in our company.
- is not flexible enough — it only applies to our cyclical assembly jobs.
- Is too complicated.
- Is too expensive.
If this sounds familiar, you should strongly consider either adding additional methods to your toolbox, or replace the method or system that’s played out it’s value with methods that better complement your needs and program maturity.
If you have a mature assessment process …
Congratulations! In the spirit of continuous improvement, what might you do to improve this process? Are there assessment methods that can provide your teams with a deeper, more specific understanding of root cause? Are there additional assessment methods that could supplement those you already use? Is there a more efficient way to manage the process, including delivering training, content and assessment tools for your team, and preparing management reports? Do your assessment methods point to solutions and good/best practices?
No matter where you are in your ergonomics process, we recommend reading our guide, 5 Essential Elements of a Successful Ergonomics Process, as a companion to this article.