Successful ergonomics initiatives are designed to drive workplace ergonomics improvements that reduce risk while making jobs easier and less painful for workers. A robust approach that accomplishes this in any workplace setting follows the risk management steps used in safety management systems like ISO 45001:
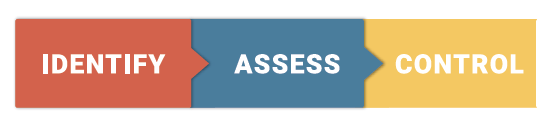
- Identify potential issues
- Assess the risk
- Control the risk
Identifying potential ergonomics issues is the first step to reducing ergonomics risk, but accomplishes little on its own – it simply gets the workplace improvement ball rolling. Robust processes to assess and control ergonomics risk are vital. Read about these steps in Ergoweb’s Guide 5 Essential Elements of a Successful Ergonomics Process.
Identifying Potential Workplace Ergonomics Issues
Potential ergonomics issues include things like awkward working postures and forceful exertions. With proper training, these can be identified by anyone in the workplace, from workers doing the tasks, to supervisors familiar with the jobs in their area, to health & safety professional conducting inspections. The three most productive activities for ensuring that potential issues are identified early in ergonomics process deployments are:
- Train workers, supervisors, and anyone else that has contact with the workplace to recognize potential ergonomics issues and how to report them
- Develop checklists of common ergonomic issues for use during activities such as safety walks, ride-alongs, area inspections, and lean production activities such as 5S audits or 3P events
- Establish straightforward methods to report potential ergonomics issues – multiple methods are recommended as communication preferences vary
Once an ergonomics improvement process is achieving sustained results and demonstrating an impact, two additional activities for identifying ergonomics issues should be considered:
- Systematically screen all jobs with a checklist of common ergonomics issues
- Survey all workers to identify tasks that they find uncomfortable or demanding
While it may feel intuitive that these activities are a good place to start, experience has shown that they can strain the resources of a developing ergonomics improvement program and be counterproductive if done too early. It’s better to start with the first three issue identification activities and ensure that the ergonomics issues they surface are addressed before launching more widespread issue identification activities. A balance of recognizing and resolving is needed – focusing too much on identifying potential problems without building the systems to resolve ergonomics issues can be self-defeating.